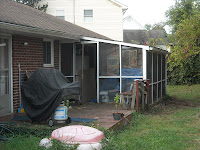
Well, we had a few weeks on hold because of various schedule issues but we are back up and running. Our contractor finished up the official drawing of the addition and then we walked it through the permit process. All in all, it could have been worse but it is pretty much the nature of the beast that 15 minutes of talking to people and filling out the required forms ends up taking 3-4 hours of waiting in various lines. However at the end of the day (
well, actually two days) we were all set. The plans were approved and we got our building permit and have it proudly displayed in the front window.
One of the early "sweat equity" opportunities identified for us in this project was the destruction of our porch and deck.
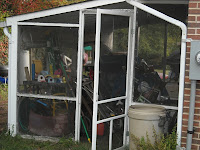
The area of the porch and deck fit entirely inside the walls of the new addition. There are partial concrete slabs that are going to be kept in place to help make the basis of the new floor in the addition. (Fresh concrete will be poured over them.) The Porch was 10'x15' and the deck was 10'x17'. Both had been built before we purchased the house and honestly, they had been built very well. They served their purposes but their time had come.
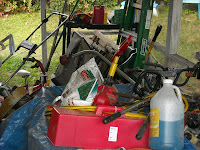
The first issue was clearing everything out of the way. The porch had turned into a bit of an outdoor junk room years ago but after last summer it had served as a temporary shed as well. As you can see, there was a lot of "stuff" that needed to go some place else before we could start wrecking anything.
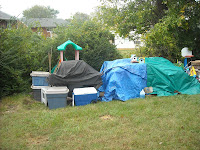
So after a little child labor, we had a lot of stuff in the trash and the rest of it under tarps. (
This did remind me that, "Oh yeah... I'm still gonna need a new shed with this is all over." D'oh.)
Being fully aware of our limitations, Mrs Toy Making Dad and myself called in some assistance...
To the Crawfish Signal!
Lucky for us,
Crawfish himself was available to pop on by in the Saab-marine with assorted pry bars and a nifty hammer or two. He was a tremendous help and honestly, there is no way we could have gotten this project done without his help. (
Seriously - Thanks man.)
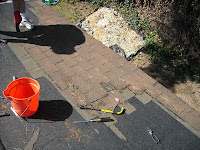
Having seen enough videos of people pulling down structures and taking the rest of the house or a bunch of windows with them, we decided that we would "unbuild" both structures as opposed to just smashing them and then cutting stuff up.
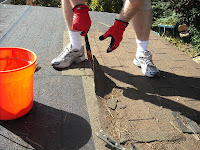 |
Act 1, Scene 2 from Tennessee Williams'
"Crawfish on a Hot Tar Roof" |
We started on the roof. Initially I carefully took each staple out of the shingles and pulled them off one at a time. I really didn't want to worry about anyone, especially our little one, stepping on those. We made good progress but as the sun came up and we got closer to the edge of the porch, we switched to pulling up big sheets at a time. The staples pretty much pulled right up and the ones left behind were no threat since we left them in the boards. The tar paper underneath was a real, ahem,
sticking point. I wonder if we had started earlier in the day if it would have peeled off easier? Live and learn.
With the shingles gone it was now, HAMMER TIME!
We hammered the plywood from inside off of the 2x4 rafters and bent them back to pry off as needed. A little difficult back at the new roof line because of the tar paper, but it went surprisingly fast. So fast in fact... that I failed to get any pictures with the sheathing in place.
Sledge hammer hits on the gutter end freed up the rafters and then we were able to twist them off of the hangers attached to the house. The far wall was made of 4x4s that were bolted together. Seriously sturdy stuff. Lacking a Sawzall (
or similar non-trademarked reciprocating saw) we took the back wall down as one piece and tossed it in the dumpster. Bye porch. (
Memories include a dinner when we first moved in, the older girls' birthday party in 1st grade, a lot of toys and whole bunch of lint from the dryer covering the floor. And spiders. Lots of spiders.)
We then turned our attention to the deck. The deck was made of 2x8's and everything was nailed, as opposed to screwed, together. Pretty much just attacked it one board at a time with pry bars and hammers.
No big surprises in the destruction although there was an odd dynamic where every board that my wife went to take up just popped up with no problem while the boards Crawfish and I attempted were all held in with tungsten or depleted uranium 17" long twisted nails. We got it done. Eventually.
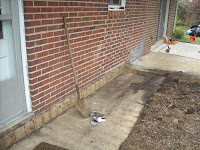
There were a couple a surprises that we uncovered though. First off we found that there was a slab poured along the back door that was covered by the deck. This may save us a few bucks when the new slab is poured for the addition floor.
There were quite a lot of patio stones used as supports and
various places around the porch and deck. There are enough that I think they
could form the basis of the floor for the new shed and we wouldn't have to pour
a slab for it instead. That would save money, but the main thing is I like the
idea of not having to break up a slab if I ever want to move the shed

We also found a concrete monkey skull. We set it on post as a warning to all the followers of the various monkey cults in our neighborhood. (
Note to self - maybe you should play with concrete more often.)
So, a second day of a few tidbits of destruction and some general cleaning up and we are set and ready for the footings to be dug and then poured. The sand is from, of all places, the sand box.
The back of the house looks huge now, so we have to fill it up with buildings and what not.